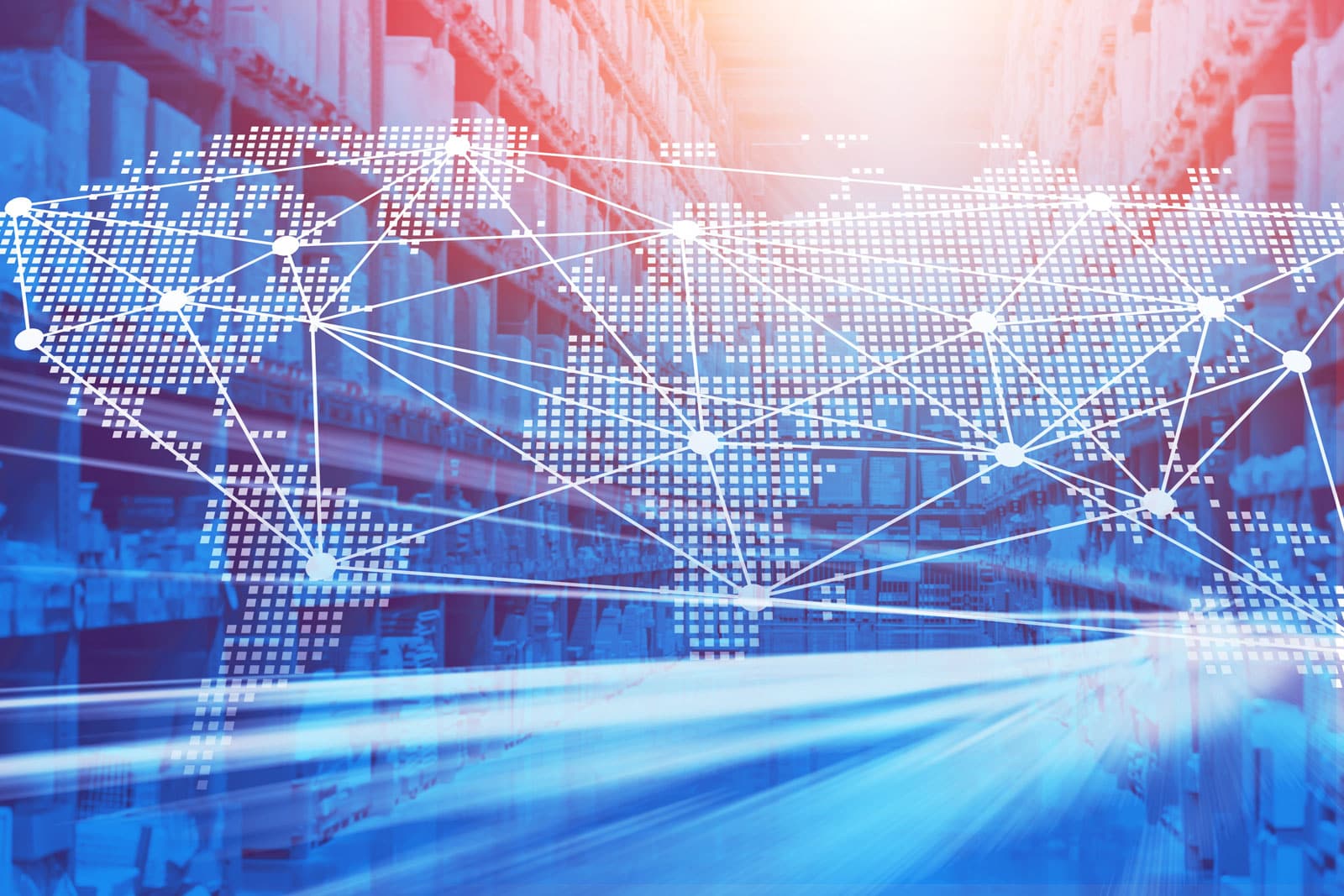
Logistics: What It Is and Why It’s Important to Your Company
The term, “logistics,” and its actions originated with the military. In the war theater, logistics applied to the process of supplying equipment and supplies to troops. Logistics as a business concept evolved in the 1950s with the increasing complexity of supplying businesses with materials and shipping out products in an increasingly globalized supply chain. Today, the business sector uses this term to describe the efficient flow and storage of goods from point of origin to the point of consumption. The supply chain is a vital part of this process, including transportation, shipping, receiving, storage, and management of all these areas. Within the business sector, logistics can be applied to information, transportation, inventory, warehousing, material handling, and packaging, disposal, and security.
Business Logistics Definitions
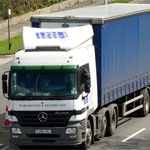
The Council of Supply Chain Management Professionals (CSCMP), the preeminent worldwide professional association of supply chain management professionals, defines logistics as “…that part of supply chain management that plans, implements, and controls the efficient, effective forward and reverse flow and storage of goods, services and related information between the point of origin and the point of consumption in order to meet customers’ requirements.” Another short CSCMP definition is “the management of inventory, at rest or in motion.” The main fields within logistics include:
- Procurement Logistics is the entire process used to select suppliers and negotiate contracts for delivery of goods or services. It consists of activities such as market research, requirements planning, make or buy decisions, supplier management, ordering, and order controlling.
- Production Logistics concerns itself with streamlining and controlling the flow through the supply chain from point of entry to the end, which is distribution logistics. Production logistics activities are related to organizational concepts, layout planning, production planning, and control.
- Distribution Logistics [PDF] is concerned with the delivery of finished products to the customer. It consists of order processing, warehousing, and transportation. Major sub-sectors within the industry include air, rail, water, and truck transportation, urban transit and ground passenger transportation, warehousing and storage, and motor vehicle repair. Logistics involve the integration of these sub sectors, including information, transportation, inventory, warehousing, material-handling, and packaging.
- Disposal Logistics, also known as reverse logistics, stands for all operations related to the reuse of products and materials. The main function of this field is to reduce logistics cost, enhance service, and save natural resources.
As the business world grew, this definition of logistics called for management, leading to the development of experts called supply chain logisticians. This type of leadership encompasses the planning and management of all activities involved in sourcing, procurement, conversion, and logistics management activities. Importantly, it also includes coordination and collaboration with channel partners which can be suppliers, intermediaries, third-party service providers, and customers.
Why Logistics is Important to Your Company

Even small businesses deal with finding suppliers, if not with transporting merchandise to a store. Small business owners also conduct distribution logistics with inventory and warehousing. And, every small business owner can tell you about how they handle reverse logistics, with returned merchandise or refusal of services. Larger businesses may deal in all four logistic fields.
In the business environment, logistics either have an internal or external focuses (inbound or outbound). Depending upon the business involved, this part of the chain can be simple or complicated. For more complicated procedures, third parties often are hired to conduct any one of the four fields within business logistics.
Third-party logistics (3PL) involves using external individuals or organizations to execute logistics activities that have traditionally been performed within an organization itself. If, for example, a company decides to export its product, it may hire a person or organization to help with distribution logistics. Today, there is a movement toward building fourth-party logistics (4PL), which integrates 3PL competencies and other organizations to design, build, and run comprehensive supply chain solutions. A 4PL general contractor would manage other 3PLs, truckers, forwarders, custom house agents, and others, essentially taking responsibility of a complete process for the customer.
Another specialty includes logistics consulting services. Firms in this industry specialize in the production and distribution of goods, from the first stages of securing suppliers to the delivery of finished goods to consumers. Such firms give advice on improvements in the manufacturing process and productivity, product quality control, inventory management, packaging, order processing, the transportation of goods, and materials management and handling. In the process, these consulting firms might suggest improvements to the manufacturing process in order to use inputs better, increase productivity, or decrease the amount of excess inventory. Consulting firms in this segment of the industry also advise on the latest technology that links suppliers, producers, and customers together to streamline the manufacturing process.
Even project management requires logistics, as one vein of this science coordinates a sequence of resources to carry out projects. Typical constraints in project management include scope, time, and budget, or the same constraints involved in business logistics. The time constraint refers to the amount of time available to complete a project. The cost constraint refers to the budgeted amount available for the project. The scope constraint refers to what must be done to produce the project’s end result.
A Global Reach
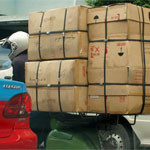
No matter the size of a business, the concern for logistics can help any effort utilize the supply chain more efficiently by cutting costs when appropriate and by avoiding waste of time and materials. If you are involved in logistics, you may know that this business is growing and that the career paths [PDF] available within this industry can range from clerks and order fillers to CEOs who manage multinational business supply chains.
Logistics is one of the main functions within a company, and the supply chain is a complex and sometime fragile global endeavor dependent on a network of independent, yet interconnected, moving parts. It requires professional management. Supply chain professionals order the product, build it, move it, ship it, distribute it, and drive the coordination processes with marketing, sales, engineering, manufacturing, finance, and information technology. In short, they make any business effort seem effortless.